Description
Die Hilgefort Gruppe ist Ihr kompetenter, zertifizierter Fertigungspartner im Anlagenkomponenten- und Apparatebau in Dinklage, Deutschland. Die Hilgefort Gruppe ist Ihr kompetenter Fertigungspartner im Anlagenkomponenten- und Apparatebau im niedersächsischen Dinklage. Vom Detailengineering bis zur schlüsselfertigen Montage vor Ort bietet Hilgefort ein umfassendes Know-how und hohe Flexibilität. Hilgefort baut Teile bis zu 7 m Durchmesser und bis zu 300 to Stückgewicht. Der Transport bis zu einem der drei nahegelegenen Binnenhäfen ermöglicht die schnelle und termingerechte Lieferung auch sehr großer Bauteile.
Seit Jahrzehnten verzeichnet das vollständig in Familienbesitz befindliche Unternehmen ein kontinuierliches Wachstum. Während in den 1980er Jahren noch jährlich 1.200 to Stahl verarbeitet wurden, konnte die Kapazität in den 1990er Jahren auf rund 3.000 to Stahl pro Jahr gesteigert werden. Heute beträgt die Verarbeitungskapazität im Schnitt bereits 8.000 to bis 10.000 to.
Tell your friends
RECENT FACEBOOK POSTS
facebook.comFilm Hilgefort GmbH Anlagenkomponenten und Apparatebau
https://youtu.be/OAZCAnXbW_M
www.hilgefort.de - www.hilgefort.de
Unsere neue Homepage ist online! http://hilgefort.de/
Made in Dinklage
rohonline
Photos from Hilgefort GmbH's post
Die Hilgefort GmbH fertigt im Auftrag der Paul Wurth Group (https://www.facebook.com/PaulWurthGroup/), die für das Design der Anlage verantwortlich zeichnet, einen Wirbler für einen Hochofen von Krupp-Mannesmann und realisiert damit eine Anlage in außergewöhnlichen Fertigungsdimensionen. Auch die weiteren Anforderungen an dieses Projekt waren hoch: nach dem Start der Arbeiten Ende Juni 2016 standen nur drei Monate für Arbeitsvorbereitung und Fertigstellung zur Verfügung. Die beiden Bauteile sind aus 15-50 mm starkem Kesselblech gefertigt. Jede einzelne Schweißnaht ist nach ISO 5817b ZFP geprüft und auch das „spannungsarm Glühen“ erfolgte bei Hilgefort im eigenen Glühofen. Ein Flanschanschluss am Bauteil musste in 7,50 Arbeitshöhe plangefräst werden. Der gesamte untere Bereich des Wirblers ist mit Edelstahl ausgekleidet und für den oberen Bereich sind Haltepunkte für Keramikfliesen angebracht. Die Montage der Fliesen selbst kann aus Gewichtsgründen erst im Stahlwerk erfolgen. Der Transport des Wirblers erfolgte in zwei Bauteilen in eine angemietete Schwerlasthalle in Voerde. Dort wurden die beiden Anlagenteile zusammmenmontiert und zum Bestimmungsort nach Duisburg weitertransportiert.
Timeline Photos
Die ASME-Zertifizierung macht Hilgefort zu einem attraktiven Partner weltweit Die American Society of Mechanical Engineers (ASME) hat im August 2016 das Qualitätssicherungssystem der Hilgefort GmbH nach internationalen Richtlinien zertifiziert. Die aufwändige Zertifizierung wurde gemeinsam mit der CIS (TÜV-Thüringen) durchgeführt. Die ASME-Zertifizierung macht Hilgefort zu einem attraktiven Partner für US-amerikanische Auftraggeber und weltweite Kunden, die Bauteile mit ASME „U” oder „S” Stamp benötigen. Allein die Vorbereitung für diese wichtige Zertifizierung betrug 7 Monate. „Ohne Einschränkungen bestanden,” erläutert Ulrich Hilgefort, Geschäftsführer des Anlagenbauers Hilgefort GmbH in Dinklage. „Die ASME-Zertifizierung hat uns Anstrengung und hohe Investitionen abverlangt, bietet aber Zugang zu dem interessanten Markt auf dem amerikanischen Kontinent und auch weltweit in der Öl- und Gasindindustrie sowie für petrochemische Anlagen.” Der ASME Code „U” und „S” regelt die Anforderungen an Herstellerzertifizierung, Qualitätssicherung, Konstruktion, Materialauswahl, Fertigung, Prüfung, Erprobung, Abnahme und Zertifizierung von Dampf- und Heizkesseln, Rohrleitungen und Druckbehältern. Die Einhaltung der Richtlinien wird unangekündigt einmal jährlich durch die ASME überprüft. Die Hilgefort GmbH zeichnet sich durch hohe Flexibilität und Innovationsbereitschaft aus. Seit der Gründung vor mehr als 160 Jahren ist das Kerngeschäft die individuelle Fertigung von Anlagenteilen. Um den Kundenerwartungen der industriellen Auftraggeber aus verschiedensten Branchen gerecht zu werden, wurde bei Hilgefort kontinuierlich investiert. „Als mittelständisches Unternehmen”, so Ulrich Hilgefort weiter, „müssen wir in weltweit sehr agilen Märkten bestehen. Das geht nur mit hervorragender Ausrüstung und qualifizierten Mitarbeiterinnen und Mitarbeitern. Die „lernende Organisation” ist bei Hilgefort nicht nur eine Worthülse.” Auf dem 7,5 ha großen Werkgelände können Bauteile mit bis zu 6,8 m Durchmesser und bis zu 300 to Stückgewicht produziert werden. Zum Kundenservice gehört bei Hilgefort die Rundumbetreuung: auf Wunsch vom Engineering bis zur weltweiten Lieferung (door to door) und dem Aufbau am Bestimmungsort. Auch Projektleiter Thomas Kolbeck stellt fest: „Anlagenbau ist nichts für Anfänger. Bei Hilgefort werden pro Jahr mehr als 200 Projekte abgewickelt. Wir beliefern die chemische und petrochemische Industrie, die Stahl- und Hüttenindustrie, Lebensmittel- und Bauindustrie sowie Bergbau oder Schiffbau mit Bauteilen wie Druckbehältern, Dampfkesseln, Trocknern, Filtern, Rohrleitungen, Drehrohröfen, Silos, Schiffbaukomponenten und vielem mehr.” Nur wenige deutsche Auftragsfertiger besitzen die ASME Zertifizierung für Druckbehälter und Dampfkessel. Damit bietet die Hilgefort GmbH eine weitere wichtige Zulassung für ihre internationalen Kunden.
Rundgang durch die Fertigung der Hilgefort GmbH
Anlagenfertigung in den Produktionshallen der Hilgefort GmbH in Dinklage
Höchste Qualitätsanforderungen bei der Fertigung von Drehrohrtrocknern erfüllt Die Hilgefort GmbH fertigte für eine Raffinierie der BP Europa SE in Gelsenkirchen zeitgleich zwei Drehrohrtrockner und zwei Sektionalkühler für eine Industrieanlage in Russland. Die Drehrohrtrockner hatten inklusive der Anbauteile, Rollenlagerungen, Heiztunnel und sonstige Anbauten ein Gesamtgewicht von ca. 150 to / Stück. Der Trommelmantel mit einem Durchmesser von ca. Ø 2,9 m und einer Länge von ca. 26,0 m wurde aus Edelstahl, Werkstoffnummer 1.4841, gefertigt. Im Lieferumfang der Drehrohrtrockner waren alle Anbauteile wie z. B. die Laufringe und der Zahnkranz enthalten. Zum Lieferumfang gehörten auch die kompletten Laufrollenstationen. Das Gehäuse des Heiztunnels für die indirekte Beheizung sowie der Grundrahmen für die Aufnahme des kompletten Drehrohres mit der Lagerung und dem Heiztunnel rundeten den Lieferumfang ab. Die Sektionalkühler hatten unter Berücksichtigung des kompletten Lieferumfanges ein Gesamtgewicht von ca. 64 to pro Stück. Die Sektionalkühler hatten eine Länge von ca. 16,0 m und einen Durchmesser von ca. 1,72 m und wurden überwiegend aus S355 NL gefertigt. Wie auch bei den Drehrohrtrocknern waren alle Anbauteile sowie die dazugehörigen Laufrollenstationen im Lieferumfang enthalten. Die Schuppendichtungen und die Austragsgehäuse für die Sektionalkühler wurden ebenfalls gefertigt und geliefert. Der Rundlauf sowie alle relevanten Funktionsmaße der Drehrohrtrockner und der Sektionalkühler wurden im Beisein eines Kundenvertreters kontrolliert. Auf Grund der tiefen Temperaturen am Einsatzort musste bei allen eingesetzten Werkstoffen einen Nachweis der Kerbschlagfestigkeit von mindestens 27 Joule bei -40°C erbracht werden. Nach der erfolgreichen Werkstattabnahme wurden die Bauteile – soweit möglich – in Kisten verpackt. Die Verpackung wurde so ausgeführt, dass eine Einlagerung über 24 Monate sichergestellt werden konnte. Die Großbauteile wie die Drehrohre, die Sektionalkühler, die Heiztunnel und Grundrahmen wurden nicht verpackt. Bei diesen Baugruppen wurden Bauteile wie Laufringen, Zahnkranz sowie mechanisch bearbeitete Flächen gesondert geschützt. Die Abwicklung des Auftrages nahm einen Zeitraum von ca. 24 Arbeitswochen ein.
Hilgefort GmbH's cover photo
Hilgefort GmbH
Quiz
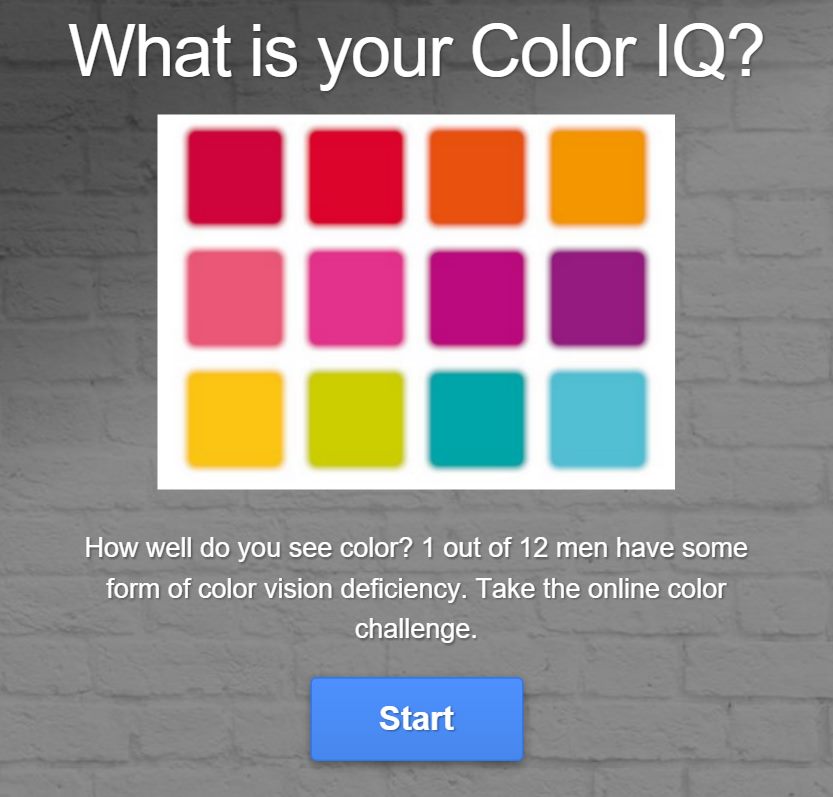