WHS Consulting Hunter
Description
WHS Consulting Hunter is a locally owned business based in Port Stephens NSW. WHSCH can assist in the Work Health and Safety needs for your business. A consultancy professional specialising in Work Health & Safety for your business.
WHS Consulting Hunter can provide you with personalised safety systems and documentation to enhance your business safety, needs, culture and most importantly budget..
Tell your friends
RECENT FACEBOOK POSTS
facebook.comTimeline Photos
What is a Workplace Induction? A workplace induction is a process that ensures new workers receive accurate and consistent information on how to perform work tasks safely. An induction should always be performed before workers or contractors perform any work tasks in your workplace. Why provide Workplace Induction? Workplace Inductions will vary depending on the type of industry specific to your business operations. A Person Conducting a Business or Undertaking (PCBU) must provide information, training and instruction necessary to protect all workers from risks to their health and safety arising from the type of work being carried out. Workers including visitors, contractors and subcontractors should be given workplace specific induction training before starting work, to inform workers about the hazards and risks they may face in the workplace and how to control identified risks – for example what to do in an emergency event. What is the Induction Process? The Induction Process is the practice of introducing new workers to your business, the type of work relevant to your industry, introduction to supervisors and co-workers, and most importantly your workplace policies and procedures. An effective induction process will help ensure that new workers: Become productive and feel part of the team to: Assist in cultural change Assist with knowledge transfer Build social networks Understand policies and procedures Understand the performance standards of their job tasks or position Understand Work Health & Safety issues relating to their task or position Understand your business culture What should you include in an Induction? An workplace induction needs to be specific to your business requirements and the requirements of new workers and should include (but is not limited to) the following – Introduction to the Manager, Supervisor or Team Leader Performance standards and worker expectations Work Times including work breaks Introduction to team members Team roles and responsibilities Introduction to other workers Your business Organisational Chart Work Health & Safety Procedures A tour or walk of your business identifying all facilities Emergency Muster Point Detail all safe work practices that are relevant to the worker/s position and responsibilities Consult worker/s on how to access Work Health and Safety (WHS) information What information should be provided at a Workplace Induction? It is recommended the following information be provided in your induction processes: Hazards and Risks specific to the workplace Control Measures for all identified Risks in the workplace Site Specific Rules that must be complied with i.e. Wearing PPE (Personal Protective Equipment) Safety Documents, Policies and Plans specific to the workplace Who to report Incidents and Hazards to and how to report them Incident, Emergency and Evacuation Procedures Site Map including Entries and Exits, Loading and Unloading areas, location of Facilities, First Aid and Security requirements. Emergency Contact Numbers and Emergency Personal i.e. First Aid Officers and Fire Warden If you’re looking for assistance with WHS/OH&S requirements specific to your industry, please contact WHS Consulting Hunter for advice on how to incorporate safety management into your business operations.
Timeline Photos
Safe Work Procedures – Do you have them in your workplace? What is a Safe Work Procedure? A Safe Work Procedure (SWP) or Standard Operating Procedure (SOP) documents the risks associated with a work task, and lists the appropriate risk control measures into a sequence of steps for performing the task or activity safely. SWP’s are most effective when developed in consultation with your workers. SWP’s / SOP’s provide information to assist your workers to perform tasks safely. These procedures can also assist in the training and orientation of new workers in the hazards of the task being performed, as well as providing your workers with the preferred way to safely perform the task/activity. They are also a useful tool when training and supervising your workers, and when responding to incident reports and changes in the workplace. What is your obligation in relation to Safety Procedures in your workplace? Persons Conducting a Business or Undertaking (PCBU’s) are required by law to provide and maintain safe working environments and safe systems of work for all persons who enter the workplace. When should you develop a Safe Work Procedure? SWP’s / SOP’s are required to be created for key work processes in your workplace that involve risk to your workers. For example, when new equipment or new chemical has been introduced to the workplace, or when existing procedures or processes are changed. Who do Safe Work Procedures apply to? All workers including contractors and volunteers must be inducted, and given regular training in relevant SWP’s / SOP’s that apply to the work task/activity to be performed. PCBU’s must also ensure that they have evidence all workers are competent to perform these procedures. How do you prepare a Safe Work Procedure? When preparing a Safe Work Procedure: - Identify the tasks and activities in your workplace that require a SWP / SOP. The tasks and activities can be identified through consultation with workers, knowledge and observation of the job requirement/s. - Perform a risk assessment to identify the most critical tasks/activities that have the highest level of risk, this will assist in determining the order of priority in developing SWP’s / SOP’s for your business activities. - Review the most critical tasks/activities to determine what hazards are associated with the task/activity. When describing a hazard, ensure the hazard is identified – for example What injury or illness might occur as a result of the hazard? How may the hazard occur and who it may happen to? - Determine how to complete the job safely. After each hazard has been identified determine if there is another practical way to eliminate the risk, if this is not possible use the hierarchy of controls. - Review the document. Once the SWP / SOP has been completed, issue a draft copy to all your workers for consultation and review. This will ensure there are no gaps and the content of the document is accurate. All workers need to approve the final draft. - Approve and issue the SWP/SOP for use. Ensure a hard copy is kept in a suitable place for reference and displayed in the work area where the procedure or task is performed. What about the Training and Competency of Workers? All workers performing a task in your workplace must be instructed, trained and educated on the hazards of the task and how to follow the SWP / SOP. Instruction, education and training is required, and must be tested to ensure the training has been effective. Under the WHS Act – the PCBU must also be sure that workers are competent in performing the task / activity and retain records of the competency. When should you review your Safe Work Procedure? - SWP’s / SOP’s are required to reviewed typically every one (1) to two (2) years or at the frequency specified on the approved document. Other considerations for review can include: - If you are requested by a worker or contractor. - If there are repeated non-compliance’s with the documented SWP / SOP. - If there is a change to a task, process or equipment in the workplace. - If there has been an incident involving the task/activity, this includes whether the incident resulted in an injury or a near miss. - If there is updated information about a hazard this information may be from an internal or external party i.e. from a worker or safety regulator. If you’re looking for assistance with WHS/OH&S requirements specific to your industry, please contact WHS Consulting Hunter for advice on how to incorporate safety management into your business operations.
Timeline Photos
Hazardous Chemicals – Are you GHS Ready? A new system of chemical classification and hazard communication is coming into effect and your business or organisation needs to be ready. The new system is called the Globally Harmonised System or (GHS) for the classification and labelling of chemicals. The new system will replace the existing system for classifying hazardous substances and dangerous goods in the workplace. Businesses in New South Wales will have until December 31 2016 to become (GHS) ready. What is the GHS? The GHS is an internationally agreed system of chemical classification and hazard communication through labelling and Safety Data Sheets (SDS). Currently different countries have different systems for classification and labelling of chemical products. These different systems make regulation of this hazard difficult, impose an additional burden on business and can impact on safe use at the workplace level. The GHS is published by the United Nations and includes ‘harmonized’ criteria for the ready classification and understanding of physical, health and environmental hazards. What are the changes? Listed below are some of the new changes such as – Signal words – There are now just two words to describe their hazard level – Danger or Warning. Hazard statement – The hazard statement communicates the chemical’s nature and severity. The language used is straightforward and familiar. For example, ‘Causes serious eye irritation’. Precautionary statement – Precautionary statements recommend measures to avoid or minimise risks of chemical exposure. The precautionary statements relate specifically to prevention, response, storage and disposal. Safety Data Sheets (SDS) – The current Australian 16-header format will continue to apply. Pictograms – There are nine (9) hazard pictograms in the GHS which represent the physical, health and environmental hazards. The nine “GHS” hazard pictograms Exploding Bomb – “Explosive” Flame – “Flammable” Flame over circle – “Oxidising” Gas Cylinder – “Gasses Under Pressure” Skull and Crossbones – “Acute Toxicity” Exclamation Mark – “Health Hazards” Corrosion – “Corrosive” Health Hazard – “Chronic Health Hazards” Environment – “Environmental” How can you prepare your business or organisation? Identify deadlines – work towards the deadline of 31 December 2016 to develop an implementation schedule. Conduct an inventory of all hazardous chemicals, identify inactive products (to eliminate unnecessary workload and reduce the site risk). Look for GHS compliant products now or reconsider the quantities you purchase. Update your chemicals and systems, including the tracking of new SDS versus old SDS – train your workers on how to understand the new labels and SDS. Is there a transition period? Yes – Australia adopted the third revised edition of the GHS under work health and safety laws. The five year transition period started in 2012. Until 31 December 2016, both old and new systems for chemical classification can be used by industry. After this date, on 1 January 2017, the SDS and labels must be GHS compliant and all workplace chemicals must be classified according to the new system. What do you need to do? Chemical manufacturers and suppliers (including importers) will be responsible for making changes and ensuring all hazardous chemicals sales are GHS compliant before the deadline. This means re-labelling and replacing the SDS for any non-GHS labelled hazardous chemicals that are supplied after 31 December 2016. Some manufacturers and suppliers are already GHS ready, and importers have been receiving GHS labelled goods from GHS compliant countries for some time. If this is the case you may only need to supply a GHS compliant SDS. All workplaces purchasing chemicals from 1 January 2017 must be GHS compliant (both labels and SDS). Consider checking this before you place an order, especially for larger purchases you are making now. Existing hazardous chemicals (with NOHSC and ADG Code labels) that you intend to keep past 31 December 2016 do not need to be re-labelled. If you’re looking for assistance with WHS/OH&S requirements specific to your industry, please contact WHS Consulting Hunter for advice on how to incorporate safety management into your business operations.
Timeline Photos
The Purpose of Safety Signs in The Workplace. The purpose of having safety signage in the workplace is to identify and warn workers who may be exposed to hazards in the workplace. Safety signs can assist in the communication of important instructions, reinforce safety messages and provide instruction for emergency situations. Workplaces have an obligation under Health & Safety Legislation to use signs where practicable to highlight a serious hazard or risk in the workplace. Compliance With Australian Standards. Australian Standards AS 1319:1994 outlines specific requirements for the design and use of safety signs intended for use in the occupational environment to regulate and control safety related behavior, to warn of hazards and to provide emergency information including fire protection information. Regulatory Signs. Safety Signs containing instructions with which failure to comply constitutes either an offence at law, or a breach of safety procedures or other directions, depending on which kind of control has been imposed at the work site or workplace. Regulatory Signs are subdivided as follows: • Prohibition Signs • Mandatory Signs • Warning Signs • Fire Safety Signs • Emergency Signs • Danger Signs • General Information Signs If you're looking for assistance with WHS/OH&S requirements specific to your industry, please contact WHS Consulting Hunter for advice on how to incorporate safety management into your business operations.
Timeline Photos
"WHS Consultation and Communication Mechanisms." Having effective Work Health & Safety Consultation and Communication Mechanisms is significant to the success of your organisation or business. For any organisation or business to operate effectively there needs to be good communication and consultation opportunities with all people working within the organisation or business. These people include Employees, Contractors, Subcontractors, Labour Hire Employees, Apprentices, Students gaining Work Experience and Volunteers. In most Australian jurisdictions it is a legal requirement to establish a formal Consultation Mechanisms. When establishing WHS Consultation Mechanisms to be used in your organisation or business it is important that you review relevant legislation to ensure that the mechanisms established are compliant with the legal requirements within your jurisdiction. Effective WHS Consultation requires the sharing of information on matters which may affect the work, health and safety of all workers. It also a requirement that all workers are given the opportunity to express their views and opinions, so that these can be taken into account when decisions about the work, health and safety of all workers are being made. Examples of WHS Consultation Mechanisms include: Establishing Health and Safety Committees Electing Health and Safety Representatives (HSRs) Conducting regular ‘Tool Box’ meetings Conducting regular Staff Meetings Effective WHS Communication is the sharing of information, policies, and procedures – and should always be a two-way process. It is important to establish effective mechanisms which suit you particular organisation or business, to allow for regular communication on work health and safety. Examples of WHS Communication Mechanisms include: Company Notice Boards Emails and Internal Intranet Systems Registers – Incident/Accident Registers Daily Pre-Start Meetings Hazard/Near Miss Report Forms Company Newsletter WHS consultation meetings with HSRs/ HSCs (Health and Safety Committees) If you’re looking for assistance with WHS/OH&S requirements specific to your industry, please contact WHS Consulting Hunter for advice on how to incorporate safety management into your business operations.
Timeline Photos
Quote of the Month!
Quiz
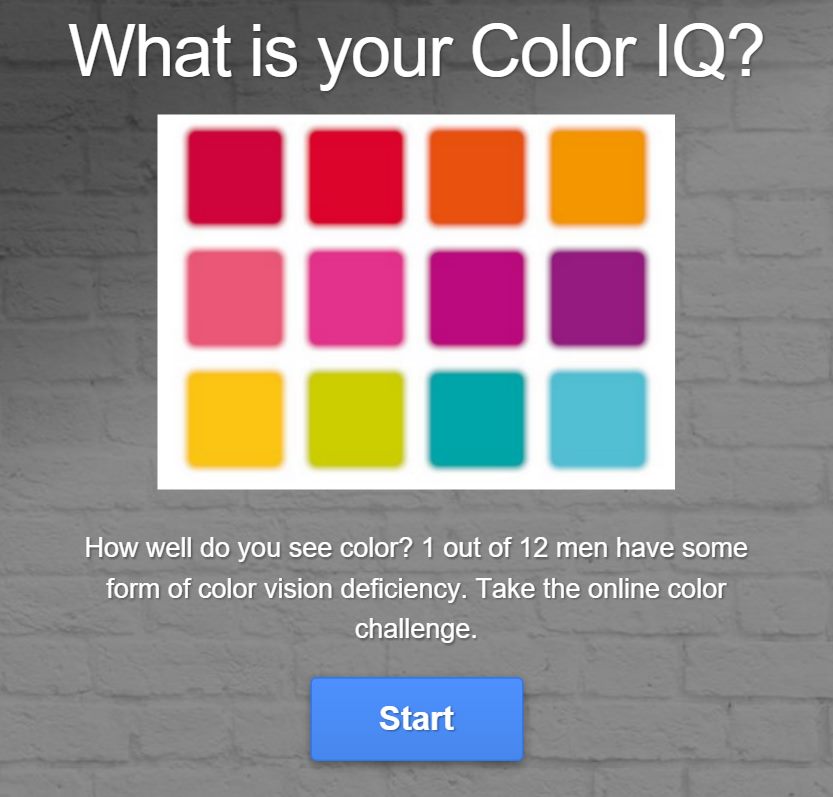